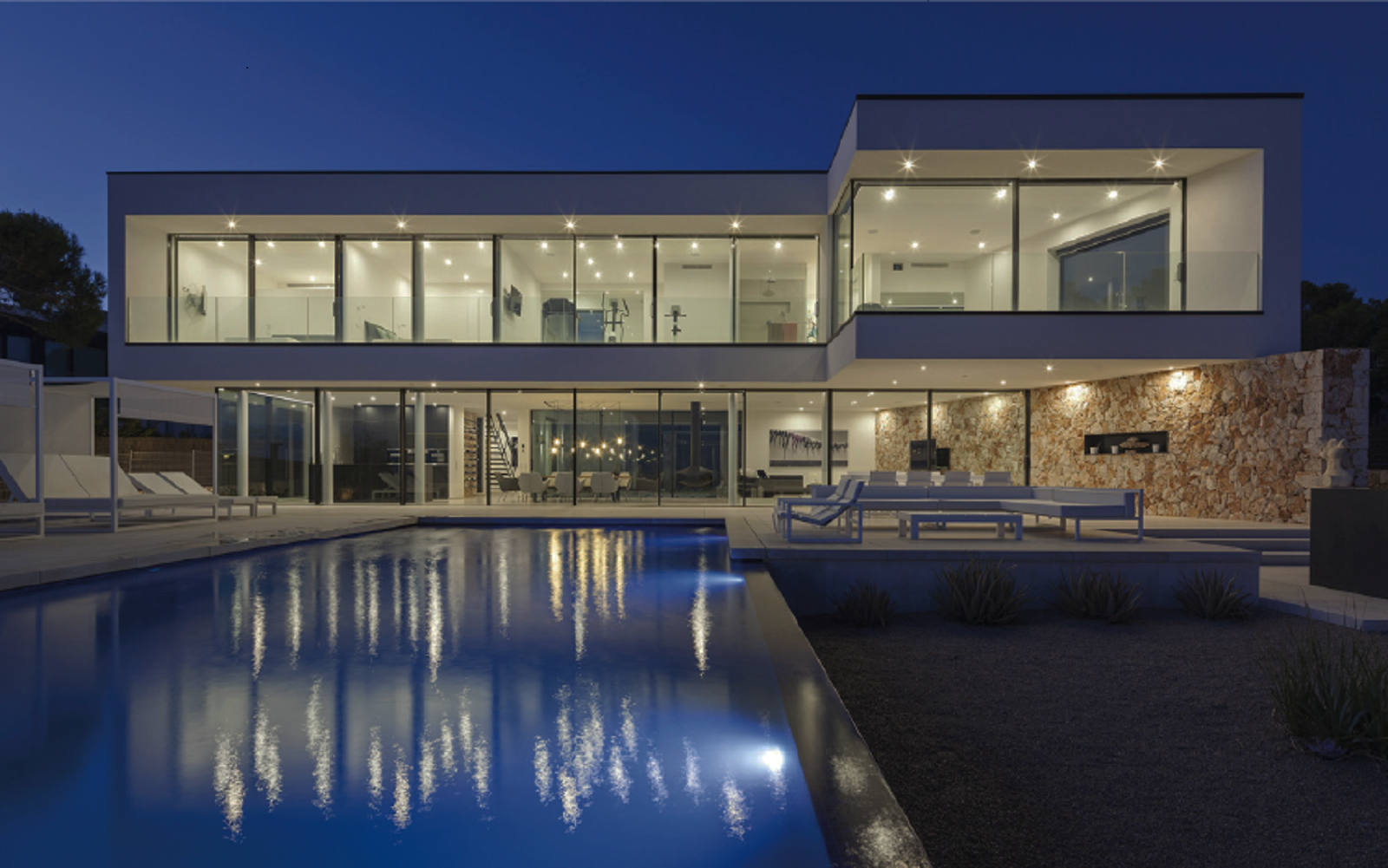
Achieving Energy Code Compliance in Glass Houses
I recently received an RFQ from a builder for a beautiful modern residence featuring an entire rear façade made up of glass. There were 10’ high sliding glass doors in nearly every room, and the great room displayed a two-story, floor to soffit curtainwall made up of oversized glass units. Upon review of the window schedule specifications however, I quickly found that the plans had a serious problem that I have seen all too frequently in this business. It was calling for thermally broken aluminum systems, using double-glazing (wes, single low-E on surface 2, with Argon (Ug=1.4 W/(m2⋅K)), and a minimum Uw-value of 1.4 W/(m2⋅K).
Code minimum for the windows, doors & skylights for this building was 1.6, however since the building had a glazing to wall area greater than 22%, the requirement of SB-12 was that the home needed to be modeled (Performance Path) to demonstrate compliance. However, the problem with the specification was that it was not possible to provide the aluminum systems as set out in the window schedule, that would also meet the Uw value of 1.4 W/(m2⋅K), using the double-glazed units (DGUs) as also specified in the window schedule.
The “Uw” value of a window, door, sliding door or skylight, is calculated (for simplicity’s sake) by combining the ratio of the U-value of the frame (Uf-value) and the U-value of the glass (Ug-value). A typical DGU, with a single low-e and argon, will have a Ug-value of ~1.4. Energy consultants know that it is possible to source window and door systems in vinyl, wood, and fiberglass, with DGU’s that will have Uw-values less than 1.4, since the energy rating of these framing systems outperforms the energy rating of the glass.
However, with most aluminum systems, the thermal value of the glass actually outperforms the thermal value of the framing and therefore, when you combine a standard glass unit into an aluminum system, you will get a combined Uw-value that is worse than that of the rating of the glass. Herein lies the problem; the specification of 1.4 selected by the energy consultant ignores the architectural design intent, and at this point the budget for the glazing portion of the building had already been set.
Before going to the homeowner with the bad news, designers always ask me the same question, ‘what can we do to meet code while keeping with the design intent, and minimize the cost impact to the owner’? The answer unfortunately is, not much. The first thing we can look at doing is to add a fourth surface low-e to the DGU which will improve the Ug-value from ~1.4 to ~1.1. However, adding these coatings is nearly the same price as a triple-glazed unit (TGU) with a Ug-value of 0.9 or better, and TGUs are also superior in sound and condensation performance, so for the small savings in cost it does not make sense to use them in my opinion. I typically will only use fourth-surface low-e’s when I am trying to keep unit weights down.
The next thing designers can look at is to switch many of the smaller windows and doors in the project over to a different window framing system. There are many other lower cost, European type systems on the market that look and function like aluminum systems, and when strategically placed it is quite difficult for the average person to see that they aren’t actually made of aluminum. This solution also provides an avenue for the energy modeler to use window averaging in their performance calculations so they can still meet code, while keeping most of the critical aluminum design elements in the project.
Whatever solution is chosen, I always urge my clients to make sure the energy modeler has the actual NFRC ratings of the selected window and door systems to use in their energy calculations so that the mechanical heating and cooling systems will be designed properly, and the rooms will be at least as comfortable as a DGU wall of glass can be. The alternative is spectacular looking rooms that feel either too hot or too cold for the owners to stay in during the extreme temperature days throughout the summer and winter.
I hope the key takeaway from this article is that designers should be aware that there is an apparent gap in the knowledge of some energy consultants that few (if any) aluminum window and door systems will meet code using a standard double-glazed unit. To prevent the problem from revealing itself at the purchasing stage, designers should request the NFRC energy performance ratings from at least one qualified aluminum window company prior to submitting the design to the energy modeler, and prior to establishing final budgets. Alternatively, consider specifying triple glazing from the outset. When the exterior wall of a room is going to be all glass, does it really make sense to use an ~R-4 insulation when ~R-9 is also an option? Sure the payback is long, but if luxury is the ultimate goal, the difference in the owner’s comfort will be immediately realized.
Disclaimer: All views expressed in this article are based on my experience in the residential aluminum window and door industry and are meant for information purposes only. The fenestration industry consists of an enormous body of science-based knowledge, and my writings attempt to distil what I have learned down into layman’s terms. I use generalizations liberally in my content and acknowledge that exceptions and elaborations can frequently be made on any given topic. I encourage readers who are informed by my articles to always seek out the advice of a qualified façade consultant prior to acting on any of my opinions. I happily invite the responses of readers who wish to expand on or correct any information or omissions.