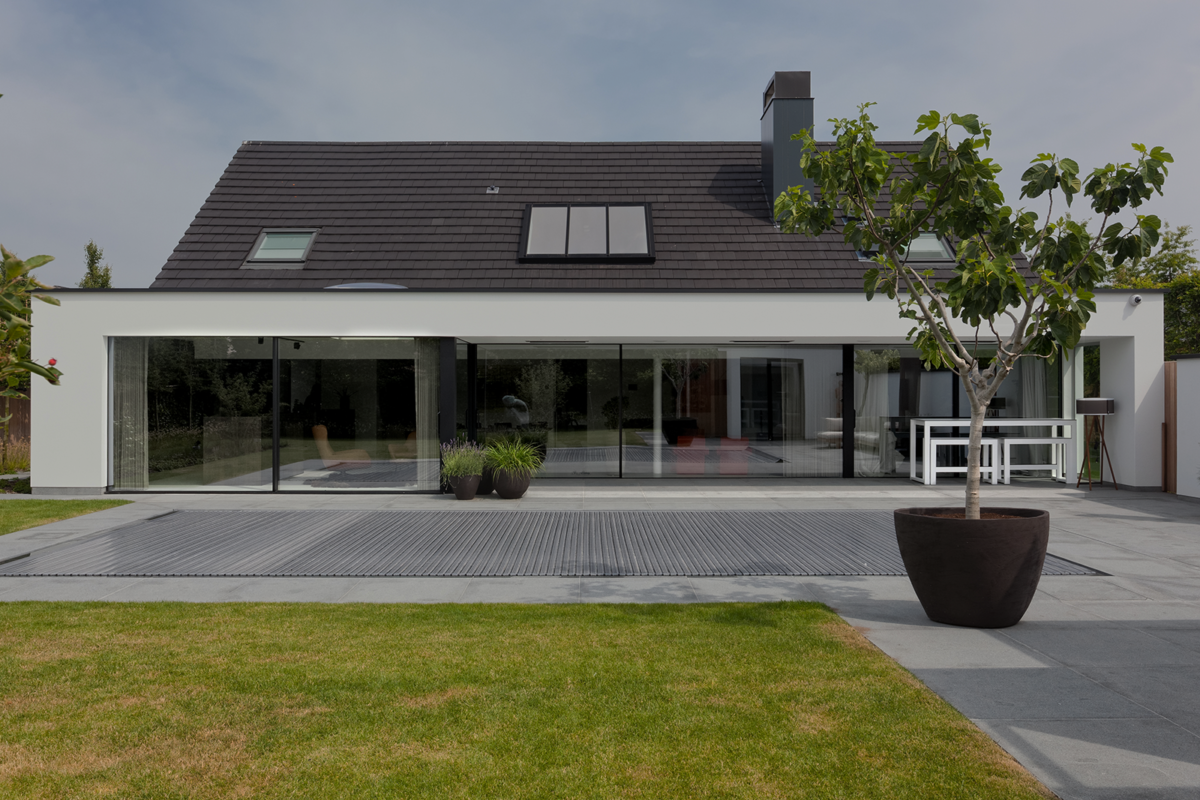
Budget Tips For Large Glazing Design
As design trends in the high-end residential and cottage industry continue moving toward large, unobstructed views, there are a few general “rules of thumb” I give to my customers to help them keep their overall glazing costs under control. These rules are of course relative to the total project scope that can significantly impact the validity of any single rule but, used as a guide they will certainly have a value-added impact on the project’s overall glazing budget.
For the purposes of this article, we will assume that all intended fenestration elements are high quality, post-glazed, thermally broken aluminum systems that can structurally withstand 25psf of pressure in larger sizes. Where element sizing is within the tested capabilities of vinyl or wood, there is no doubt that high-end aluminum systems will not be able to compete with them, where bottom line pricing is the final consideration.
KEEP AREAS OF GLASS UNITS UNDER 50 SQUARE FEET
The most basic of the cost-saving rules that I give to architects, is to keep the total size of any given glass unit to less than 50 square feet, where most commercial suppliers of glass units will increase their cost by a factor of 1.5 or more. This does not mean that any window or sliding glass door needs to be less than 50sq’ in total, rather that you should consider adding a mullion for any windowpane that is unnecessarily greater than 50sq’. Also, as the glass area increases, so too does the structural wind loading on the unit, which may result in an increase of the thickness of glazing required. The thicker the glass, the more the cost, especially when the associated weights call for increased hardware performance and specialized equipment for handling.
DO NOT ADD UNNECESSARY PROFILE OR HARDWARE
The inverse of the 50sq’ rule is also true. Adding mullions just for the sake of design adds costs that can substantially add up over the scope of a project. This is due to the additional material and manufacturing labour required to produce them, while realizing only a negligible reduction in total sq’ glazing area. This problem is compounded whenever glass unit falls below a minimum size set by the manufacturer, and you end up paying for units by the piece and not by the square foot area. Worse than adding transom profile to a window is to add sash profile and operating hardware just for the sake of symmetry. Operating elements are often more than triple the cost of a fixed field so to save money, avoid adding a bank of 5, side by side, 2’ roto-operated awnings, 8’ feet in the air that the customer is unlikely to ever use.
AVOID ADDING JUMBO UNITS
When unit sizes over 50sq’ are necessary, designers should always attempt to keep one dimension of the glass unit under 8’. Units with dimensions greater than 8’ in both directions require specialized equipment to produce and only a handful of manufacturers in North America have made the investment. There are also other associated costs these manufactures face such as increased material prices, increased wastage, and increased risk, to name a few. You should also consider that jumbo units are likely to look (read) differently than the rest of the glazing on the project and it may be necessary to have the jumbo unit manufacturer fabricate other units around the jumbo for aesthetic reasons alone. There is nothing more spectacular than standing behind an insulated glass unit 130” x 236” looking over a pristine landscape, but suffice it to say that specifying “Jumbo” glazing into a project comes at a huge premium to be sure.
CONSIDER INSTALATION AND UNIT REPLACEMENT COSTS
You should always consider the physical location of the large glazing from an installation and replacement perspective before drawing it into the design. I once was asked by a designer if I would consider installing some large windows in a cottage that had been abandoned on site by another supplier. As it turned out, the glazing left to be installed was overhanging a sheer cliff and the installation was going to cost substantially more than the supplier and customer had budgeted on. Since the most spectacular view in a building is sometimes located in the most difficult place to access, Architects should always consult with a qualified glazing company before selling their client on their big glass vision. Beyond the initial logistics and cost of installing the unit, one should also consider what will be the costs of replacing that unit should a failure occur in the future.
FINAL COMMENTS
When properly done, adding oversized glazing in residential projects can really add to a feeling of spaciousness and luxury however, customers should expect to pay more for it. I have seen many projects designed in such a way that the initial fenestration budget was less than half of my estimated selling price, and the conversation quickly turns to how can we “VE” the project?
Most good fenestration companies will offer some sort of design assist to architects early in the project concept phase and whenever possible I urge clients to take advantage of it. I like to keep the initial price as low as possible and if the appetite of the owner is to spend more to get more, it is a much easier exercise than getting them to decide to give something up. In the budget development phase, consider pricing two options, fist as lowest possible pricing scenario and second as your “dream world” option. This will at least give you a range of pricing to work with and help you avoid the last-minute redesign scramble when the client starts to see the initial fenestration numbers coming in.